Quickly detecting and repairing methane leaks is crucial as we work to reduce our greenhouse gas (GHG) emissions and continuously test and deploy new methods to mitigate methane emissions.
In the U.S. Lower 48, we rely on a variety of tools and techniques as part of our well-established leak detection and repair (LDAR) process to find and address leaks with solutions that best suit each site. In addition to traditional audio-visual-olfactory inspections and the use of optical gas imaging (OGI) cameras, recent advancements in technologies are providing additional monitoring solutions.
We have been conducting pilots of new technologies at several facilities within the Lower 48 to determine effectiveness and scalability for these next-generation detection and quantification technologies. This has included a range of possible technologies from ground based to aerial with each providing different strengths for different monitoring situations.
“The goal is to identify and repair leaks faster, resulting in faster mitigation of emissions from our operations,” said ConocoPhillips’ Senior Geoscience Fellow, Khalid Soofi.
Continuous monitoring
In 2020, we led industry by working with Scientific Aviation to develop and test continuous methane monitoring devices at select Lower 48 facilities to further enhance LDAR. Building on previous experience with plume modeling using planes and drones, Scientific Aviation and ConocoPhillips worked to design a ground-based sensor system to detect leaks.
The SOOFIE, which stands for Systematic Observations of Facility Intermittent Emissions, sensor is a relatively simple and cost-effective metal oxide sensor that continuously records several methane measurements a second. Three to four sensors are placed on poles around a facility for better coverage and effectiveness under variable wind conditions.
Any elevated measurement of emissions picked up by the SOOFIE sensors are integrated into an automated machine learning system that considers details such as equipment location, distance, wind speed and direction to identify the most probable emission source. By using information and lessons learned from our operations, Scientific Aviation was able to modify the system to improve its capabilities quickly. If the system suspects a leak, an alert is sent to operations personnel for investigation and repair.
Testing has shown the sensors to be more effective at quickly detecting leaks commonly found using OGI cameras. While the sensors are wind dependent and require internet connectivity to operate, they have been tested against other more established and expensive equipment and show similar accuracy.
“Unlike other detection systems we use, which are deployed on a more scheduled basis, these sensors allow industry to shut down large emission sources quickly,” said Steve Conley, Scientific Aviation’s President and Chief Executive Officer.
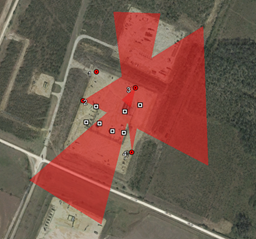
The SOOFIE system allows us to mitigate methane emissions by identifying leaks in real time and fixing them more quickly than other technologies which only sample on demand. We evaluated the risk associated with assets across our operations and deployed continuous monitoring sensors to locations based on the potential for emissions and proximity to neighbors. We have installed approximately 360 devices covering over 100 locations, with a focus on continuous monitoring of our larger Lower 48 production facilities. We are continuing to evaluate system durability through weather events in the field and to optimize the number of sensors required at each location. We are also aligning methane data with our operations data to better understand the correlation of leaks and equipment functions. Implementation of continuous monitoring has given our operations people on the ground the opportunity to better understand how equipment performs and it is changing the way we manage and mitigate anomalous leaks. Just as a continuous focus on safety has changed behavior and made us a safer company, we believe the continuous detection of emissions will change the way we think and handle methane leaks.
ConocoPhillips, Scientific Aviation and six other energy companies have also joined together to further study the best way to deploy continuous methane monitoring technology to detect emissions and assess quantification uncertainty. Referred to as Project Falcon, the data and results from SOOFIE sensors will be made available to the industry, regulators and the public through publication in a peer reviewed journal.
In addition, we have also tested cameras at several facilities to allow operators to conduct virtual site visits. These cameras, which are also equipped with sound, provide a complete view of the well facility. Operators can monitor for lifted hatches on tanks, smoking or unlit flares, releases from pressure safety valves and spills. The integrated operations center (IOC) team can also view the well site immediately after a remote monitoring alarm is triggered to assess the situation and prioritize dispatching an operator.
Aerial monitoring
We have tested several different types of aerial monitoring technologies that enable routine monitoring over a larger area and number of facilities. Airborne systems are an established way of providing a better overview of emissions from an entire facility and geographic area.
Drones are an established technology that have proven to be very effective in detecting the source of leaks and quantifying emissions due to their low flying altitude. By flying a vertical plane pattern downwind of facilities, they can pinpoint the source of emissions and quantify the leak. While very accurate, we only use them in specific circumstances as they are difficult to execute across hundreds of facilities due to economics, drone-related flight regulations and the special resources required to use them. View more about drone technology.
Airplanes with mounted sensors fly over facilities to detect leaks based on the relative amount of methane and wind direction and speed. If leaks are suspected, operations personnel take over to verify and fix the leak. The sensors can detect smaller leaks, but their effectiveness can be diminished in areas where other facilities are in close proximity, like the Permian Basin.
Satellite-based detection technology is another large-scale leak detection option, and its effectiveness has improved rapidly. We are currently testing the technology at a range of assets where it works well at detecting larger leaks such as unlit flares, but also has limitations in areas where facilities are in close proximity. Recently launched satellites are showing promise in providing better imaging, detecting smaller leaks, and providing more frequent monitoring of specific facilities.
Combined, these technologies have helped build a stronger and more robust monitoring toolkit as we work to reduce emissions across our operations.