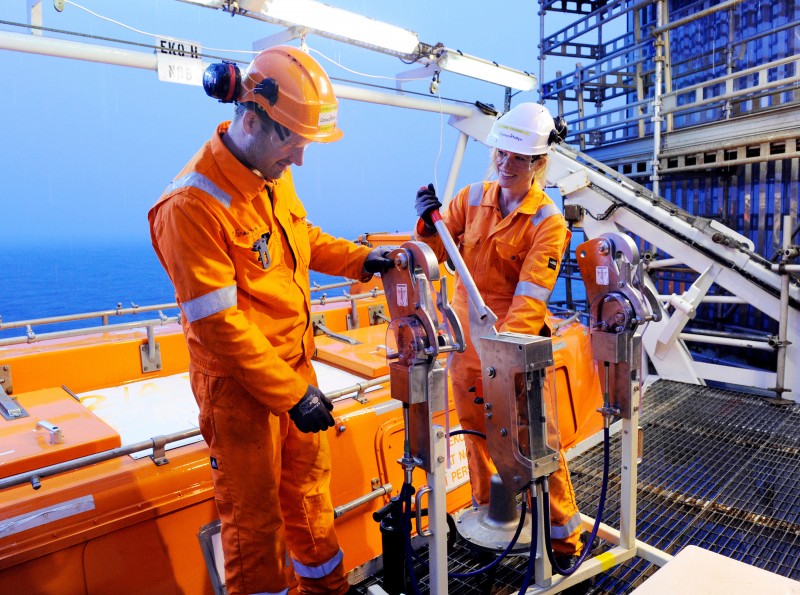
Bridging the gap between how work was planned versus how it was performed helped Norway record their safest year yet in 2018. The effort started in 2013, when process isolation and crane and lifting activities (which can all lead to serious injuries or fatalities) were identified as major accident risks. A team of skilled offshore workers and leaders was established to assess the challenges and opportunities associated with the tasks. It was quickly determined the activities had complex requirements, room for interpretation and a lack of common understanding.
First, the team simplified requirements, ensuring that our Life Saving Rules were clearly integrated. Workers and leaders were trained through facilitated sessions. Handbooks detailing essential requirements of job tasks were also developed and made easily available at the worksite. The team then made informal but focused verification trips offshore to understand how the original design and proposed method/requirement work together. A crucial element of this process was candid, honest conversations with the workforce, letting them tell the story of how work actually occurs. Integrating their input into the proposed method and equipment changes was an important part of building a culture supportive of the new safety initiatives as well as a valuable source of information about processes and logistics. Workforce involvement in safety improvement planning has been ongoing; more than 100 suggestions were submitted for the recent sixth update of the Process Isolation Handbook.
In 2017, another team was established, relying on the same methodology to understand weak signals from incidents and near misses in the well bay of offshore platforms, an area with high activity where an incident can have significant consequence.
Key aspects of that work include:
- Interface between operations and well operations.
- Alignment of requirements between groups.
- Assessment of routine operations, both simple and complex.
- Involvement of multiple contractors.
As a result of the offshore verifications, requirements were simplified and several procedures were removed. The team created a handbook that is used as the basis for conversation and noted that the quality of the conversations has improved. The effort helped lead to a decrease in total incidents and improved near miss reporting. Life Saving Rules verifications and details from near misses shed light on new areas for learning and improvement.
“Fundamental to the success of this work is the involvement of the workforce. By getting them onboard and together making improvements to the system they are working in, we achieved great ownership and sustainable improvement,” said Jan-Arne Johansen, general manager, Norway Operations.