STORY HIGHLIGHTS
- Alaska, Canada field trials to determine if 3D printing can ease supply chain challenges, reduce costs
- Company's Global Production experts develop API standards for additive manufacturing
- Learning & Competencies team keeps employees abreast of latest projects, tech developments
Spare parts are sometimes hard to come by on Alaska's North Slope.
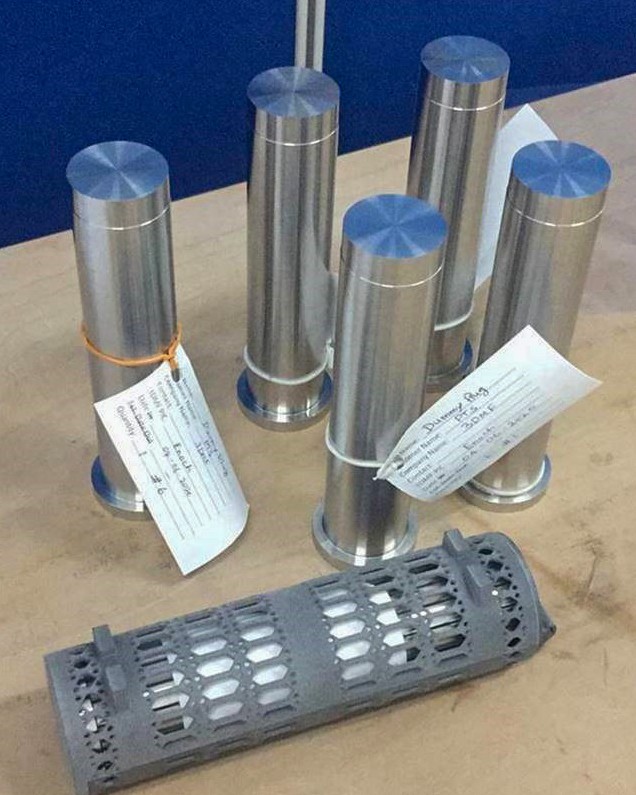
Take burner plugs, for instance. These consumable parts, found within ConocoPhillips’ original gas turbines at Kuparuk (a 40-year-old field), aren’t manufactured anymore.
So, when one of these components wears out — they eventually succumb to what’s known as heat erosion — it’s a challenge to replace them. In such remote locations, lead times for certain equipment can stretch from 30 to 60 weeks.
To remedy this supply chain issue, Alaska business unit teams — in collaboration with ConocoPhillips’ Global Production experts — have been testing 3D printed burner plugs in its Ruston gas turbines at Kuparuk.
The plugs are printed using Inconel 718, a high-strength superalloy with a nickel-chrome base material resistant to high pressure and extreme temperatures. In the case of these outdated burner plugs, which are no longer covered by intellectual property laws, it’s possible to go from a set of drawings to a printed object in about a week and then have it shipped to the field location.
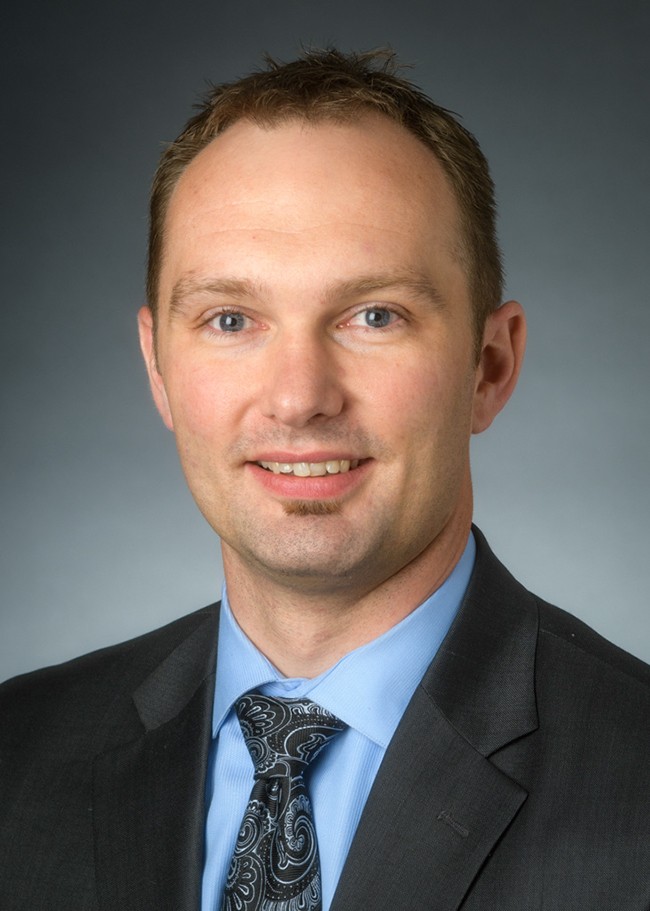
“So, you’re taking something that would traditionally be a 30-week thing down to a two-to-three-week thing,” said Curt Andersen, an Instrument, Control and Electrical Engineering Supervisor for the Alaska business unit. “And so far, the printed plugs are working fantastic. They're performing as good, if not better, than our conventionally made plugs.
3D printing
3D printing, also known as additive manufacturing, is the construction of a three-dimensional object from a CAD model or a digital 3D model. In 3D printing, material is added together, layer by layer.
Common materials used in 3D printing:
- Plastics
- Powders
- Resins
- Metal
“This was an opportunity for us to trial something that had a lot of potential advantages to it, and also use this as data for the rest of the company. For us, this is a new method of manufacturing that comes with a lot of questions, such as what does the part look like when we put it in service? How does it act? Does it act like another piece of metal that was rolled, forged or cast?”
In another Alaska pilot project, ConocoPhillips teams have partnered with an original equipment manufacturer (OEM) and additive manufacturers to 3D print choke cage valves, which are flow control devices used in water injection wells.
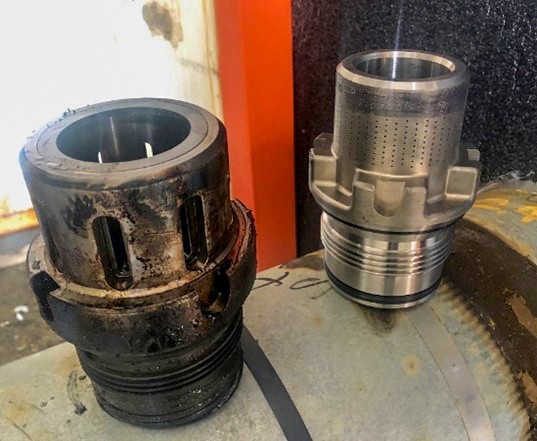
In this instance, the Alaska team identified numerous choke valves obsoleted by the OEM. The solution: retrofit the existing valve bodies with 3D printed valve cages made of Inconel 718.
“We’ll be able to extend the life of the choke valves using an optimized design,” he said, “replacing parts only when we need them. With additive manufacturing, you don't have to go out and buy a whole new valve, plug or whatever the piece."
These 3D printing trials, he said, exemplify the Alaska business unit's continual search for innovative, cost-effective ways to maintain and optimize its operations.
“Additive manufacturing is an exciting technology with extreme potential to not only maintain 40-year legacy assets and equipment," Andersen said, "but also improve the performance of those assets in a cost competitive way."
On Alaska's North Slope, ConocoPhillips operates the Kuparuk River Unit. In such remote locations, ConocoPhillips is testing 3D printing to see if it can ease supply chain logistical challenges.
Benefits of 3D printing
- Avoid supply chain disruptions/lag time
- Faster production
- Print parts on demand
- Digital inventory rather than warehousing parts
- Better quality, design flexibility/enhancements
- Print parts closer to their point of use
- Reduces inventories, warehousing costs
The benefits of additive manufacturing are enticing, he said.
“For an operation like the North Slope of Alaska, because we are so remote, and because it can take such a long time for things to get there, we maintain a fairly large warehouse of parts, especially the ones that we consider critical. That comes with a lot of extra costs. There’s the cost just to simply store them and have the space for them but there’s the ad valorem tax that we have to pay for just having that on the shelf.
“So, in an utopian future view, if you have these parts in a digital format, if you have the drawings and the design criteria for them, you could simply ship them to a partnered print shop, produce them and have them in a much quicker fashion than worrying about do I need to order this thing 30 weeks out in order to have it on the shelf in time to do this maintenance activity. So, you could create a lot more certainty within the supply chain itself and also potentially significantly reduce costs in terms of warehousing and inventory.
"We need a good bit of information to execute a successful and legal print. Part information like metallurgy and service conditions, a design drawing/3D model that is either not controlled under intellectual property or can be used with permission, a manufacturer that can meet the need."
Key contributors to the Alaska field trials include Joel Brandt, mechanical engineer; Joe Wingerter, rotating equipment engineer; Scott Ure, rotating equipment engineer; Jennifer Ingram, facility engineer; Kuparuk Valve & Central Shops Personnel; and Carlo De Bernardi, subject matter expert, Corporate Additive Manufacturing & Valve .
Canada field trial
In British Columbia, ConocoPhillips is field testing 3D printed water-valve parts at its Montney water hub.
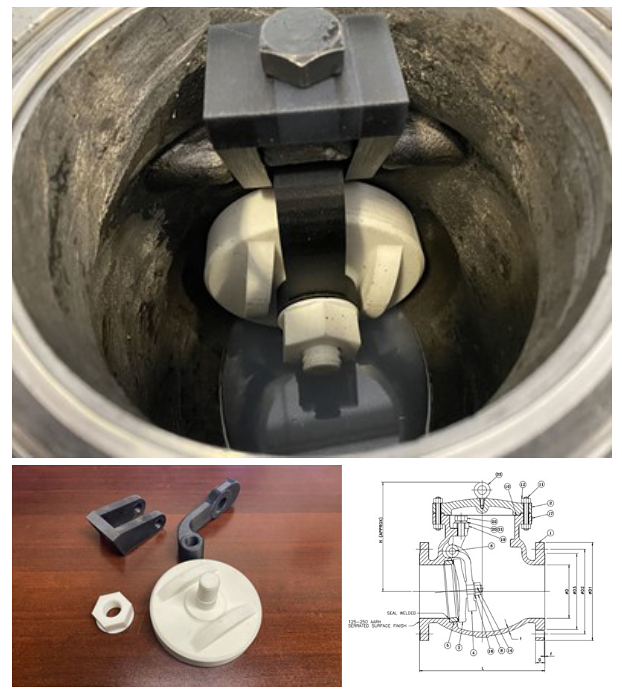
In this example of additive manufacturing, the Canadian business unit has been trying to resolve corrosion issues with a swing check valve trim assembly used at its water treatment facility, which retreats saline produced water for re-use in future fracs.
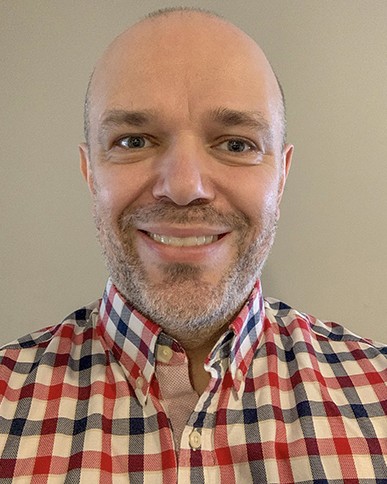
The team improved the internal design of a 4” swing check valve and developed a 3D printed polymeric version of it. If the 3D printed valves prove worthy, the business unit is planning to retrofit more than 20 valves with the same solution. Not only will this solution prevent business unit personnel from having to replace the entire valves with a more expensive super duplex stainless steel (SDSS) solution, but it will also enable them to print the internal valve parts in only days compared to the 32-weeks lead time associated with the SDSS solution.
“The Montney is a tremendous asset for the ConocoPhillips Canada business unit,” said Lee Osness, Senior Facilities Engineer. “This asset carries its own unique set of challenges, and we look for innovation in these challenging spaces. It’s all about being creative. It’s about noticing a problem that needs to be fixed.”
Developing standards for additive manufacturing
The journey to 3D printing has not been without its challenges.
Learning organization
To increase workforce awareness across ConocoPhillips’ business units and stimulate innovation for new technology, the Learning & Competencies team is hosting virtual sharing sessions on the company’s latest pilot projects, including 3D printing.
“These sessions allow our employees to stay abreast of our latest projects and industry developments,” said Kelly McLure, senior advisor, PetroTech Learning. "ConocoPhillips is participating in industry-leading pilot projects with our internal experts leading the way."
In these examples, the initial challenge facing the team was the absence of industry standards around additive manufacturing. Instead of waiting for someone to fill that gap, Carlo De Bernardi, staff engineer, Valves, put together a group of 184 experts across disciplines and industries (energy, aerospace, defense) in 2019 and presented a proposal to the American Petroleum Institute (API) to create the first Oil & Gas Standard for the qualification for 3D printed metallic components.
After two years of work, the API Standard 20S was published in October 2021, defining qualification criteria and elevating the confidence level on additive manufacturing. Almost in parallel, De Bernardi identified the need for a similar standard for 3D printed polymers and the API 20T task group was born, led by his colleague Enzo Savino, staff engineer, Non-Metallics.
Such innovative work is helping push the boundaries of what's possible.
"We are also working on 3D printed polymeric ball valve internals to replace stainless steel in corrosive environments, a large metallic pump impeller and a first stage fuel nozzle," Savino said. "And Hernan Rincon, Staff Engineer, Materials, is leading the characterization of additive manufacturing metals in corrosive and sour service environments."
Creating a digital inventory
To deploy additive manufacturing on a large scale, ConocoPhillips’ next step will be to enable a digital inventory concept. With a network of approved 3D printing vendors and OEMs, ConocoPhillips can create digital twins of spare parts and print them on demand, close to the point of use. This solution will reduce inventory costs and improve supply chain resilience by avoiding logistics challenges with traditional manufacturing. It will also reduce Scope 3 emissions.
To achieve this goal, ConocoPhillips is working to have more of its business units join this effort while collaborating with its Technology and Supply Chain teams for scale up and integration aspects.