“It’s all coming together,” said Jonathan Kiesewetter, swiping through his iPhone to review construction photos of a Permian Basin tank battery, an optimized greenfield facility pilot.
The tank battery, known as Redtail 2A, is designed to reduce Scope 1 and Scope 2 greenhouse gas emissions while targeting competitive capital spend through a reduction in installed equipment count.
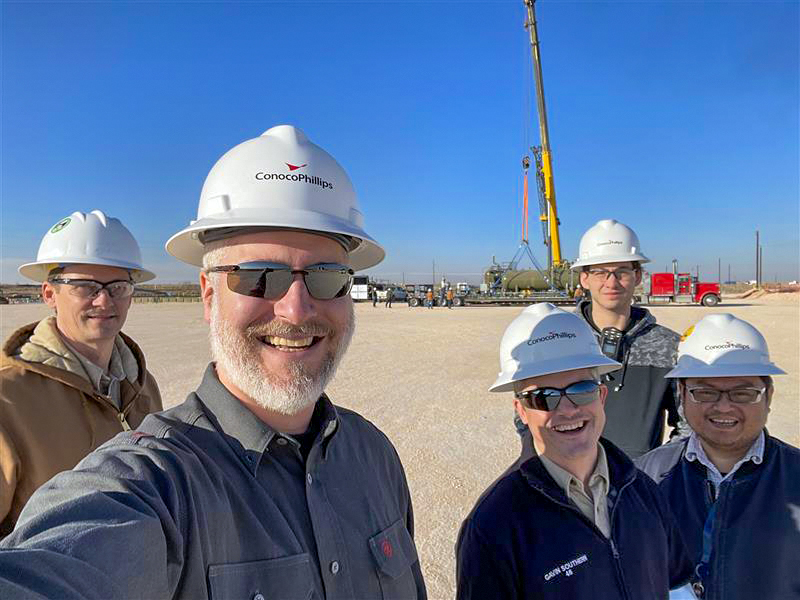
“This particular tank battery is about an hour outside of Carlsbad,” explained the staff process engineer with Global Production Facilities Engineering, just back from inspecting the New Mexico facility. “We’ve got equipment being placed, and it’s scheduled for start-up in April.”
Located in the Delaware Basin East and developed in close collaboration with Global Production, the Permian business unit, Gulf Coast and Rockies Capital Projects, and Lower 48 Sustainable Development, this central tank battery is one of the latest technical projects that Jonathan has contributed to as part of his role within Global Technical Functions (GTF), where he helps with technology development, project development and operations support. GTF is a centralized set of functions consisting of petrotechnical and operations experts providing support for ConocoPhillips’ global operations, with Global Production being a key subgroup.
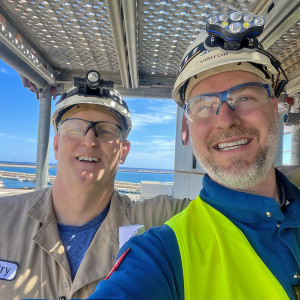
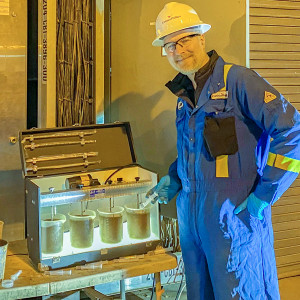
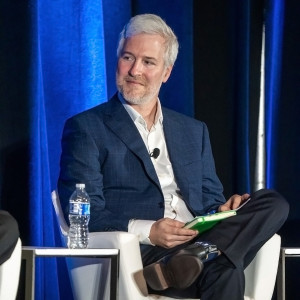
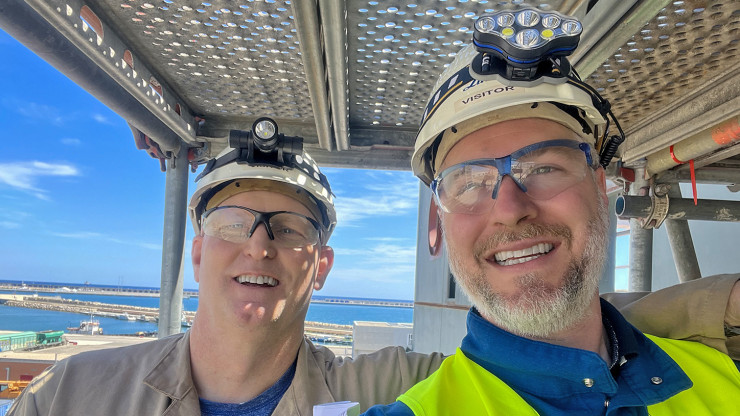
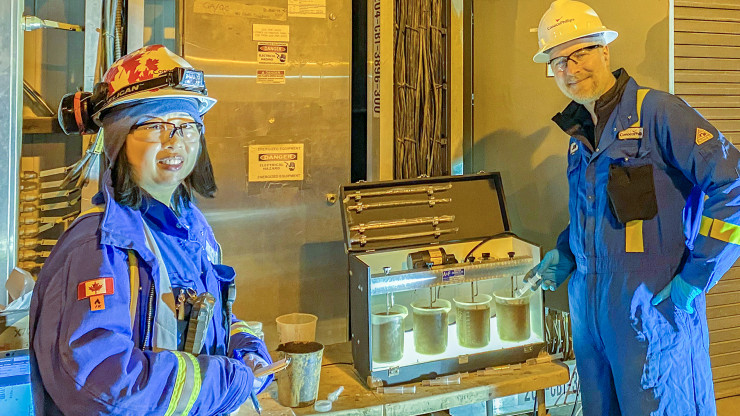
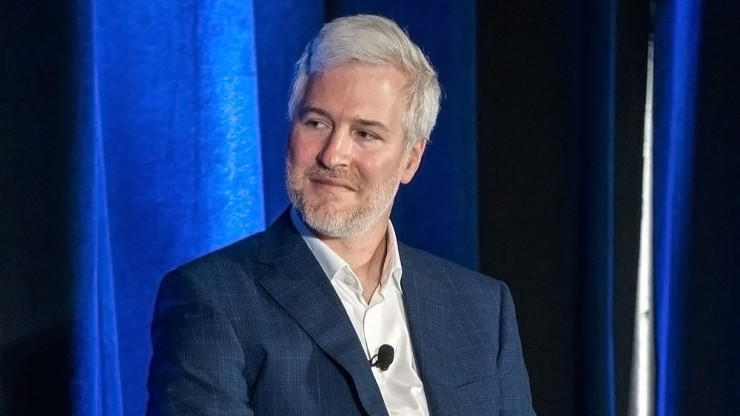
During his 10-year career at ConocoPhillips, Jonathan has tackled a variety of complex technical challenges. His expertise spans water treatment and reuse, heat transfer, and process engineering,
Process engineers like Jonathan are problem solvers, progressive builders and inventive thinkers. They design and optimize ConocoPhillips’ facilities and plants to ensure they run safely and efficiently.
“I’ve always enjoyed making things and conducting science experiments,” said Jonathan, who graduated with a degree in chemical engineering from The University of New South Wales (UNSW) in 2010. “If you’re excited about something, it’s not a chore to work on it.”
If you’re excited about something, it’s not a chore to work on it’
From Australia to Canada
After graduating from UNSW, Jonathan joined CH2M Hill, working first in Sydney and then in Winnipeg, focusing on water treatment and wastewater management projects.
Years later, while in Calgary, Jonathan met with Greta Zornes, a former colleague from CH2M Hill in Sydney who had since joined ConocoPhillips, to discuss a job opportunity at ConocoPhillips.
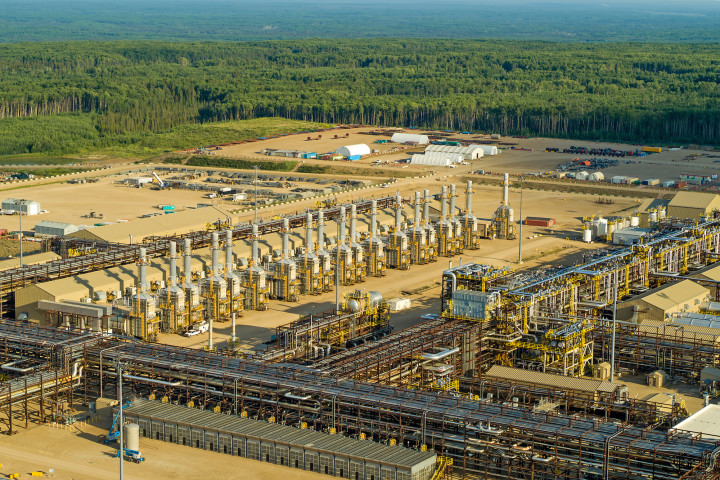
It was only after meeting with Greta that Jonathan gained a deeper understanding of both the similarities and the unique challenges related to water treatment in the oil and gas industry. His expertise in water management and engineering made him an ideal candidate, and it was an opportunity he could not resist. He joined ConocoPhillips Canada in October of 2014, starting as a process engineer supporting Surmont.
Based in Calgary, Jonathan joined the oil sands technology and optimization group for Surmont. He focused on optimizing steam generation and water treatment at the asset, where steam is used to melt the viscous bitumen into an emulsion that is about 75 percent water.
“We separate the water out of this emulsion, then we treat the water so we can generate steam with it and then reinject it into the ground,” Jonathan said. “Produced water treatment is a critical component of the Surmont facility, occupying a large fraction of the facility footprint.”
In 2017, Jonathan moved into a new role at Surmont CPF1 as a contact engineer. He played a pivotal role in supporting the day-to-day operations of the central process facility and its wells and pipelines, honing his skills in troubleshooting and contributing to a variety of dynamic projects.
Pioneering developments at Montney
Building on his experience at Surmont, Jonathan transitioned to the company’s liquids-rich Montney asset in 2019. There, he focused on process engineering and water treatment for its gas plant, joining in time to contribute to the final design stages of the first phase of the Montney facilities.
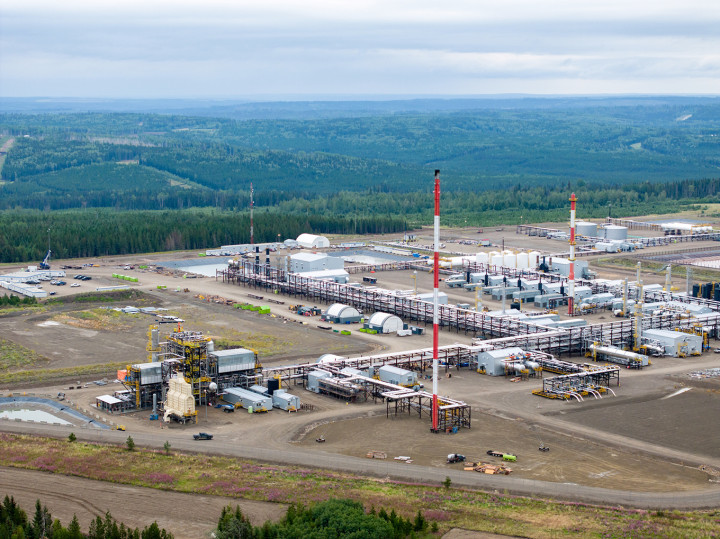
With Jonathan’s extensive background in water treatment, his transition couldn't have come at a more opportune moment. At this time, ConocoPhillips water expert Ramesh Sharma was in the midst of designing and building a water treatment facility for the C-11-K gas plant, based off learnings from the Permian Basin. The water treatment facility maximizes water recycling by treating and storing produced water for reuse in completions, reducing the amount of fresh water required for the development. Jonathan had the opportunity to witness and contribute to the final stages of the facility’s design, commissioning and startup.
"It was awesome to see it all come to life," Jonathan said.
In addition, Jonathan learned about the completions process used on the Montney wells, working with Completions Fluid Specialist Paul Carman in GTF on friction reducer selection.
“The selection of completions chemistry has a big influence on how to treat the flowback and produced water from the wells,” Jonathan said.
As part of those learnings, Jonathan, Ramesh and Paul co-submitted a patent application detailing how friction reducer chemistry impacts water chemistry and treatability. They also outlined methods for treating produced water contaminated with specific friction reducers.
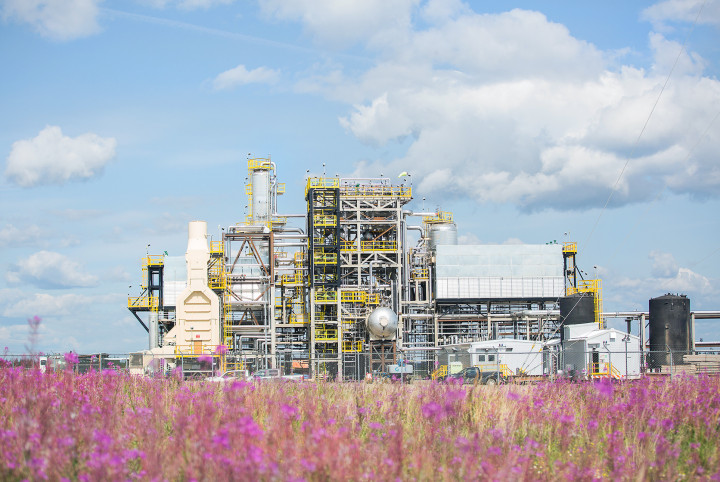
Moreover, Jonathan collaborated with Principal Process and Modeling Engineer Dale Embry and other professionals to develop the condensate recovery unit (CRU) at Montney. This facility transforms off-specification condensate into valuable, marketable products using distillation and blending of cuts.
“We successfully patented that process,” Jonathan said. “Late last year, that patent was officially approved. Over the span of about three years, we were able to go from a concept development and simulation exercise to actually seeing it built and operational.”
Unlike most field facilities that typically produce only gas and oil or natural gas liquids (NGL), the Montney C-11-K facility stands out by generating gas, NGL and a dense condensate stream. Due to stringent product quality requirements for condensate, the CRU was developed to fractionate the stabilized dense condensate into a light oil and sales condensate stream, both meeting required product quality specifications for sale into their respective product pools. The CRU process adds complexity and additional pretreatment processes beyond those seen at a typical gas plant, such as desalting and overhead corrosion management processes, but has been successful in mitigating product quality constraints that posed a risk to the Montney development.
As Jonathan was wrapping up the CRU project, he transitioned to the GTF organization in Houston in May 2023. “My role in GTF has been an incredible opportunity to branch out, understand how the company operates globally, and share my insights across various business units,” he said.
Collaborating with the Global Water Sustainability Center
As part of his GTF duties, Jonathan has been collaborating with the Global Water Sustainability Center (GWSC) team in Doha, Qatar, a team led by GWSC Manager Samer Adham. Together, they are evaluating various novel solutions and emerging technologies to enhance water treatment and recycling across multiple ConocoPhillips operations, including the Permian and Montney.
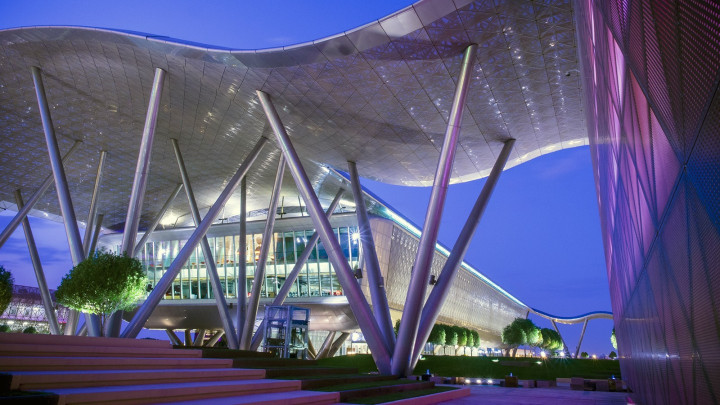
“We are excited about the new technologies we’ve introduced this year,” Jonathan said. “Our focus now is on boosting their technology readiness level and figuring out the best ways to scale them up for broader application.”
Adham praised Jonathan’s dedication and enthusiasm for his work, highlighting the process engineer’s technical expertise in water management and treatment.
"Our collaborations with Jonathan also involve partnering with academic institutions to ensure their experiments are conducted under relevant field conditions,” Adham said, “maximizing the applicability of their research to ConocoPhillips’ operations.”
This work involves exploring ways to expand the use of treated produced water beyond the oil and gas industry, aiming to unlock new possibilities and applications for this resource.
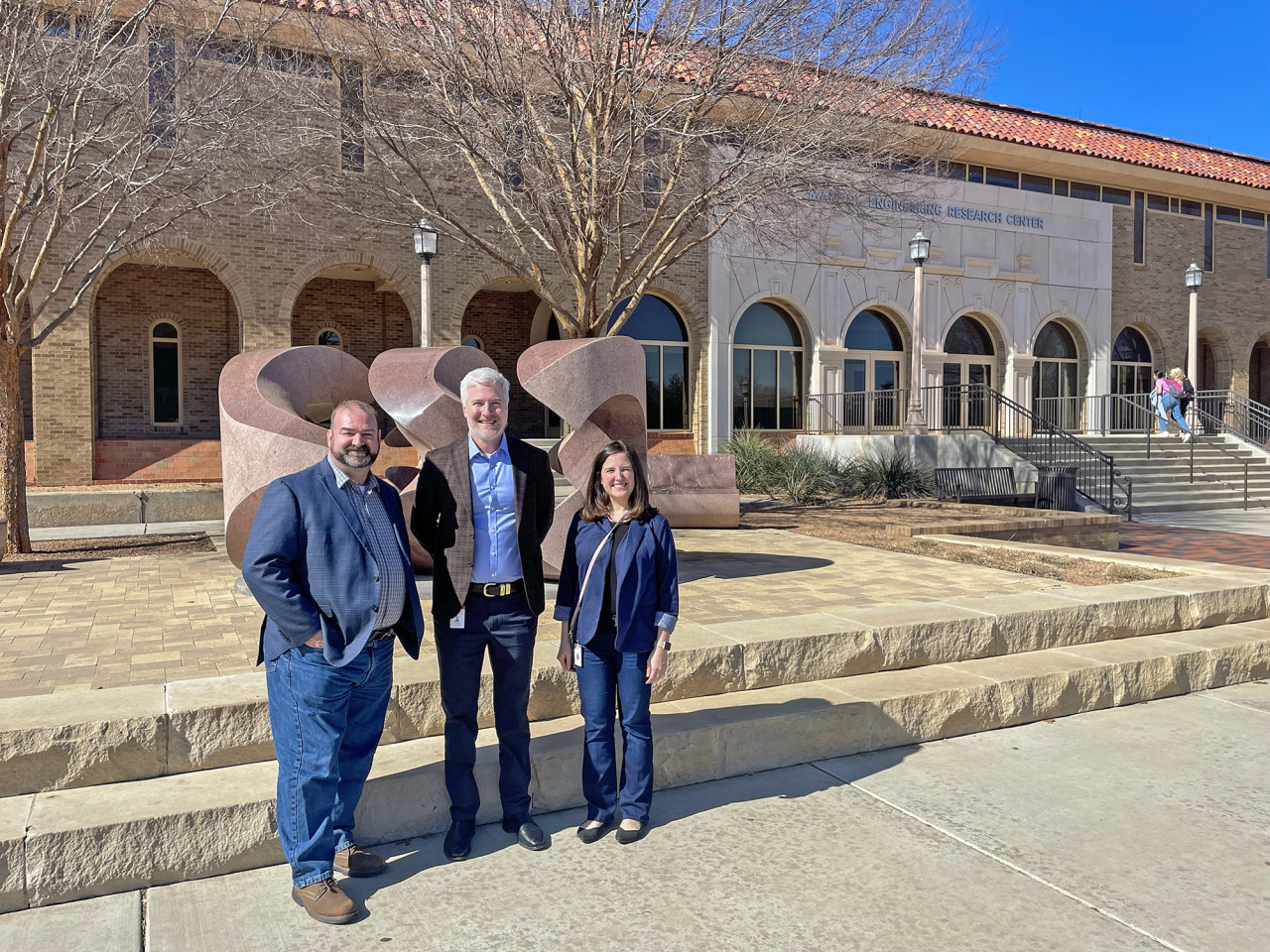
Model rockets and home-brewing adventures
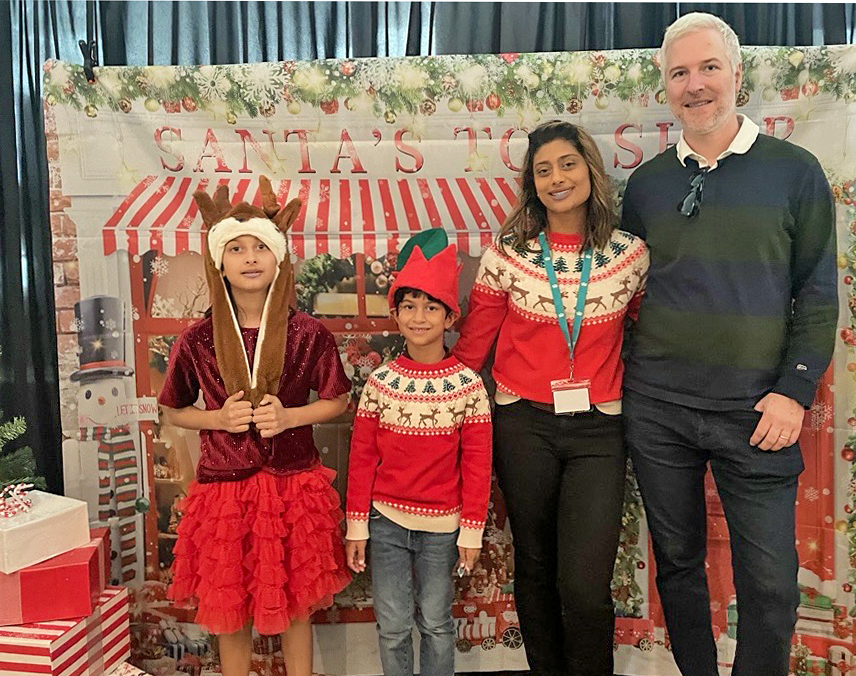
In his spare time, Jonathan has rekindled his love for building model rockets, now sharing this exciting hobby with his 6-year-old son. It's a passion he first discovered while attending a Rudolf Steiner School in Sydney, where he excelled in mathematics and chemistry. Additionally, Jonathan continues to indulge in his long-time hobby of brewing beer, a craft he’s been passionate about since his university days.
He’s also embarked on an inspiring new water-related challenge: reef aquarium keeping. “It’s a work in progress. The fish are thriving, but it’s definitely a challenge. It’s like mastering a whole new realm of chemistry.”
“Jonathan’s practical experience in designing and commissioning hydrocarbon and water treatment projects truly sets him apart. Notably, Jonathan combines practical operations and engineering skills with a researcher's passion for science and chemistry. He is equally comfortable interacting with field operations and university professors. His extensive experience in the Canadian business unit is incredibly valuable to Global Technical Functions. Jonathan not only understands operational priorities and practical limitations but also recognizes the potential benefits and opportunities new technologies can offer."
"Jonathan is a true polymath of process knowledge, constantly evolving and expanding his expertise. He has an insatiable curiosity to understand how things work, always digging deeper rather than just accepting advice at face value. When he learns something new about a project, he eagerly shares that knowledge with his colleagues, fostering a culture of continuous learning and collaboration.”