ConocoPhillips Innovation Director Liz Jolley drives a Tesla Model 3, the electric vehicle a reflection of her futuristic mindset.
“Tesla took the car business and totally rethought it,” she said.
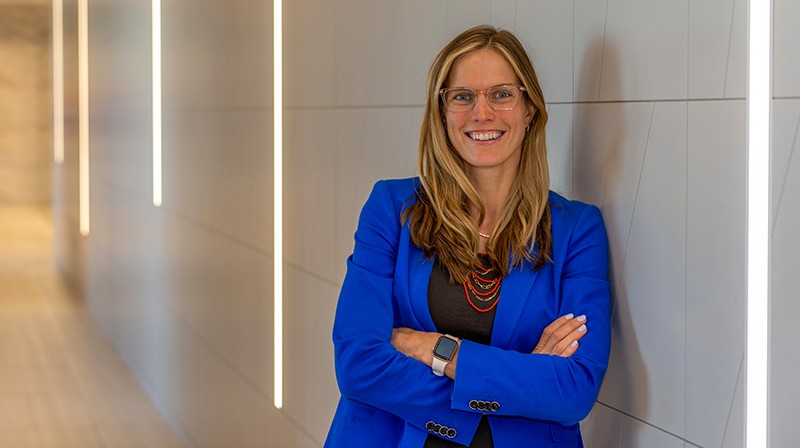
Jolley finds inspiration in visionary companies like Tesla and SpaceX, even online eyeglass retailer Warby Parker, where the mother of three buys her eyeglasses. Such companies are reimagining what’s possible. ConocoPhillips, she said, is doing the same for the oil and gas industry.
“You have to keep innovating, or you get left behind," Jolley said. "Innovation is about being open to opportunity. It’s like a race, where everybody is running and getting faster and better. Innovation is more important than ever."
With her magnetic personality and trademark smile, Jolley is leading the innovation charge at ConocoPhillips. She collaborates with the company’s global workforce, encouraging them to ask, “What could we do better? What could we simplify?”
“To maximize our investments,” she said, “we need to leverage and adopt what's proven to drive down our cost of supply.”
With a drilling and wells background, Jolley has seen firsthand the amazing innovation and technological advancements the company has made during her 18-year career at ConocoPhillips, including extended reach drilling on Alaska’s North Slope.
“ConocoPhillips is no stranger to innovation,” she said. “We’ve been doing it for decades.”
Collaboration nirvana
Fuel, the company’s solutioning software platform, allows employees to capture, track and share ideas across the globe.
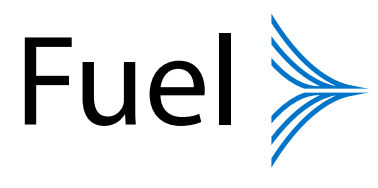
This treasure trove of ideas and adoptable technologies enables the company to determine which ideas to say yes to, and to pinpoint solutions that are scalable, impactful and add value. Serving as an idea pipeline, Fuel reduces redundancy while providing transparency, empowering employees to adopt successful ideas and avoid repeating mistakes.
“Instead of every business unit creating their own solution for a problem and recreating the wheel,” Jolley said, “they should be looking to other business units to see if others have had the same problem and how they solved it, asking ‘Can we adapt and adopt?’”
Reducing maintenance costs in the Eagle Ford
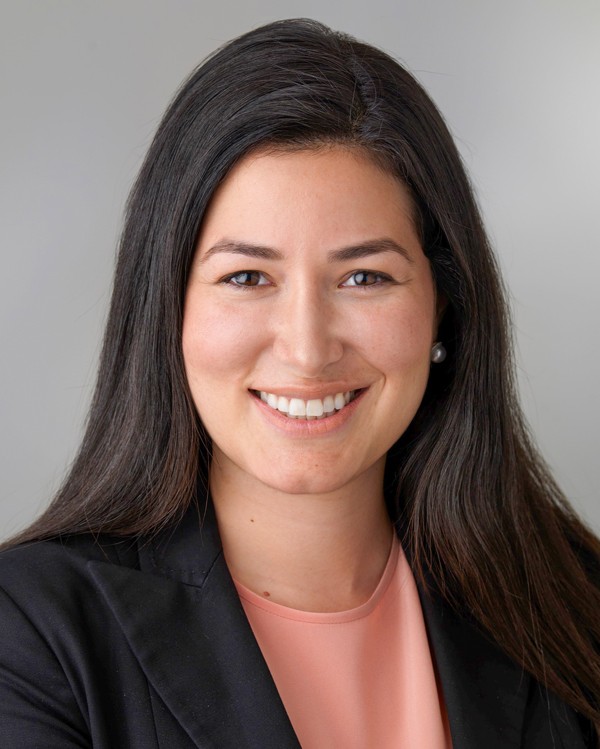
As part of its defect elimination program, the Eagle Ford Operations team wanted to explore different hydrogen sulfide scavengers to reduce equipment maintenance cost.
The Operations team searched Fuel and discovered the Norway business unit, in collaboration with Global Production, already had a solution for a similar issue, one that was close to adoption and could possibly be leveraged in the South Texas asset.
“Instead of having to start from zero, we were able to conduct a quick search in Fuel and find that Norway just completed a similar effort," said Mariana Rincones Huff, Operations Integration Director. "We are hoping that leveraging their work will reduce our research, testing and solution implementation time.”
Mixed-reality inspections in Indonesia
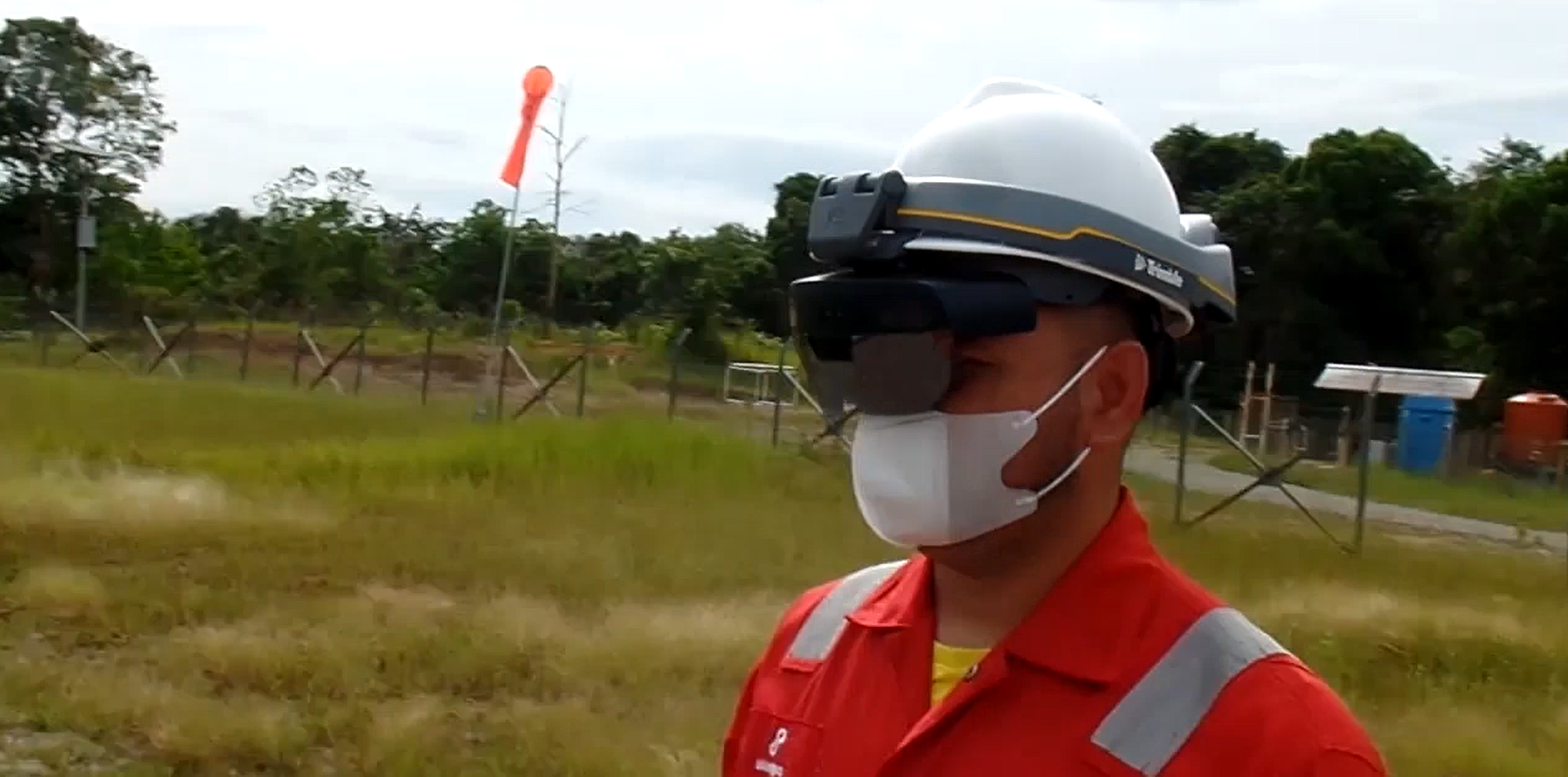
When the Indonesia business unit needed to conduct facility inspections with limited workers on site because of the COVID-19 pandemic, employees turned to Fuel for ideas. There, they discovered Microsoft’s HoloLens technology had already been trialed, and they were able to use the mixed-reality smart glasses for their inspections.
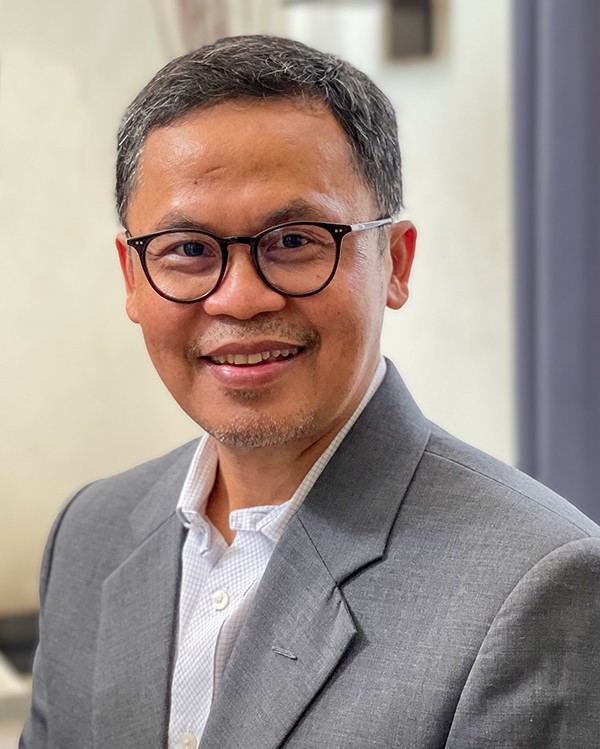
“HoloLens came just in time given the challenging situation, such as during the current pandemic where travelling is limited, to maintain our operation efficiency,” said Wawan Gunawan, asset integrity manager, Indonesia. “Thanks to the Fuel platform and corporate Emerging Digital Technology team, we have been able to adopt a potential solution to our challenge that’s been proven in other business units. HoloLens technology has enabled seamless virtual collaboration between our engineer in the office and field inspector on site to make important real-time decisions for our field operations.”
Learnings flow from Canada to Alaska
When Alaska business unit employees were looking to adopt a new redlining Management Of Change (MOC) tool, they turned to Fuel to learn more about a software their colleagues in Canada had already adopted and proven.
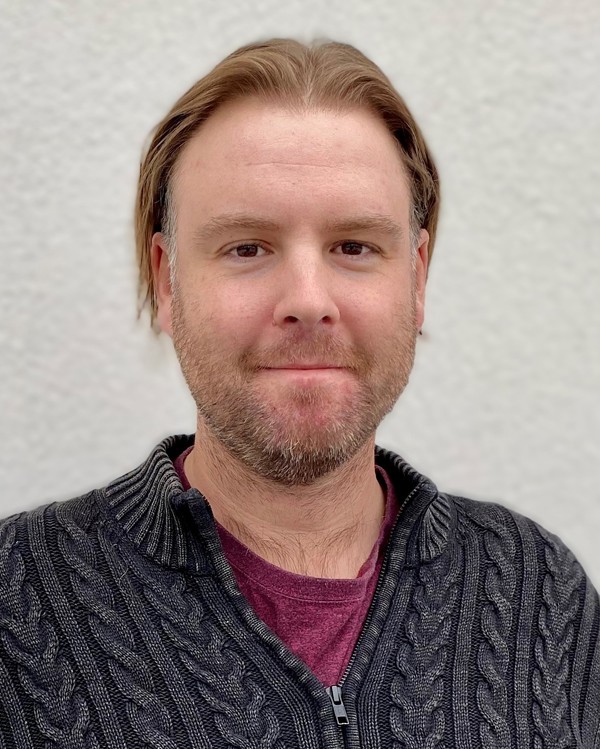
Traditionally, the redlining process, which involves numerous document revisions, can be a time-consuming and tedious endeavor, often requiring manual changes by hand. To streamline their redlining process, Canada implemented a software by Bluebeam that improves markup and document collaboration.
“Necessity is the mother of invention, and cost of supply has served as this necessity for us here in the Canada BU,” said Brenan Wotherspoon, projects quality assurance lead. “The adoption of an electronic redline tool has meant a significant improvement for us in terms of cost, quality, risk and time."
The Canadian team, which seamlessly transplanted the redlining software into their existing procedures, was able to share their learnings via Fuel.
"This has been so successful because it was a relatively simple tool to introduce," Wotherspoon said. "It’s technology that already existed and didn’t need to be developed, and it fit into our current processes."
Fostering an innovative culture
In addition to managing and championing Fuel, Jolley plays another vital role: fostering an innovative culture by moderating workshops and facilitating brainstorming exercises with different groups, encouraging them to transform the business and drive adoption.
We can’t be closed-minded and think we have all the answers. We have to be learn-it-alls, not know-it-alls.
“Everyone at ConocoPhillips plays a role in innovation," she said. "Innovation is similar to safety. Safety isn’t owned by one person in the company, it’s everyone’s responsibility.”
Successful innovation requires collaboration, curiosity, trust and vulnerability. Employees must have an environment in which they feel comfortable challenging each other’s ideas and speaking their minds. Such diversity of thought accelerates the creative process.
“In such an atmosphere, you can make better decisions,” Jolley said, “because you’ve already wrestled with all the different risks and concerns that people have. We can’t be closed-minded and think we have all the answers. We have to be learn-it-alls, not know-it-alls. We have to stay curious and live in the discomfort of that ambiguity. In the future, it’s not just going to be one technology that changes things, it’s going to be thousands of them.”