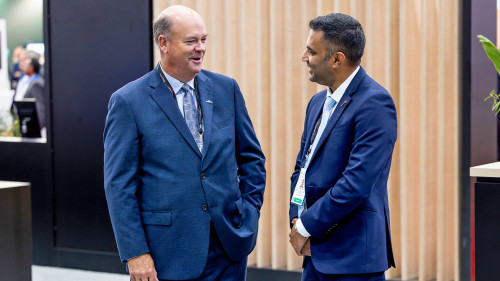
Strategic moves / How ConocoPhillips is expanding its global LNG business
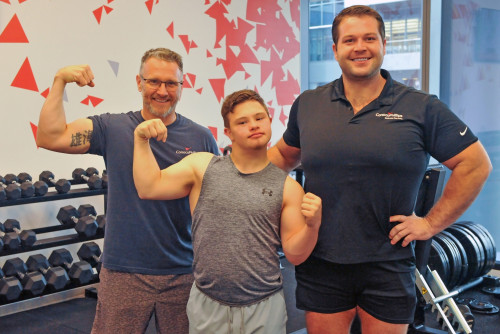
The power of inclusion / Cameron’s fitness journey
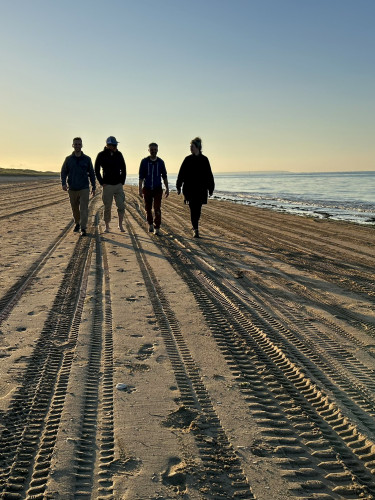
SPIRIT Values
The words are not proprietary to our company but the combination and the acronym are pure ConocoPhillips.
2025 Rodeo Run
Nearly 12,000 people participated in the 2025 Rodeo Run on March 1 in downtown Houston. Sponsored by ConocoPhillips, the annual event benefits the Houston Livestock Show and Rodeo Educational Fund.
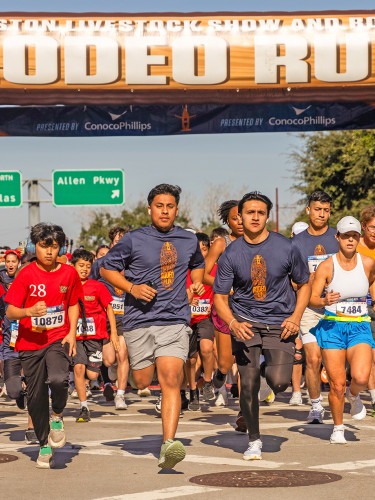