Operated by ConocoPhillips, the Australia Pacific LNG (APLNG) export facility consistently achieves over 99% reliability, the result of a robust maintenance schedule.
“We operate a world-class LNG facility in Australia with a rigorous 52-week maintenance schedule that is planned and scheduled into our work activities to minimize downtime and ensure the reliability of the facility,” said Jan-Arne Johansson, president of the Australia business unit.
APLNG — a joint venture between ConocoPhillips Australia (47.5%), Origin Energy (27.5%) and Sinopec (25%) — is complex, with approximately 137,000 maintainable components.
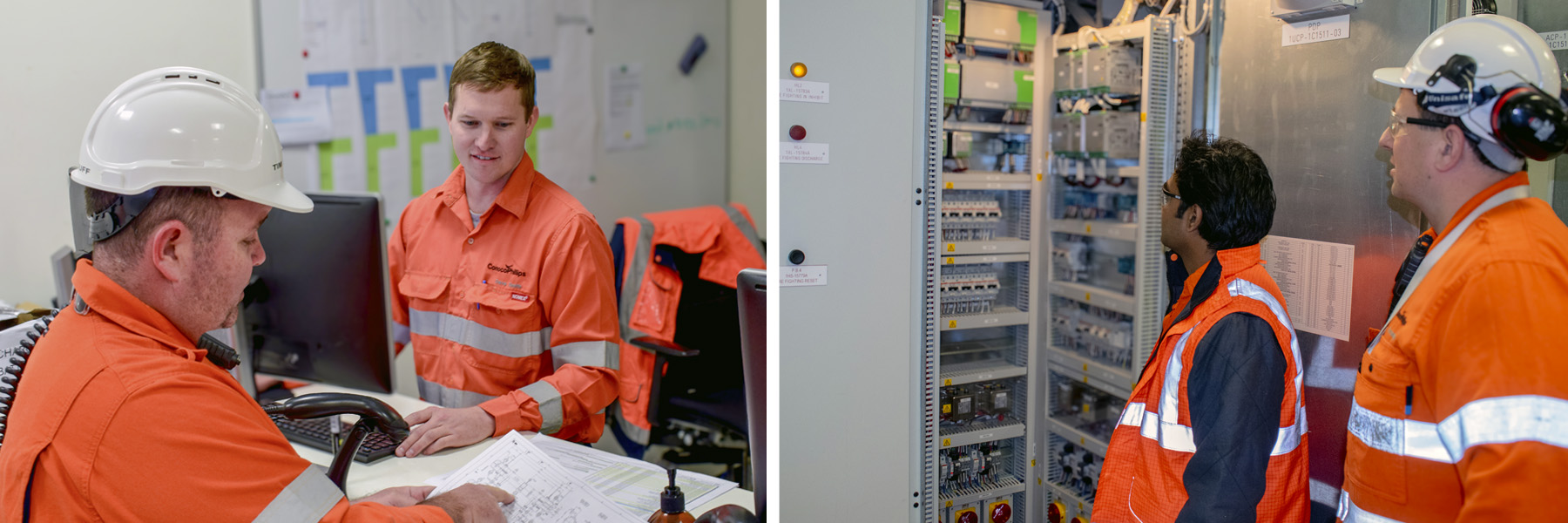
Using the latest technology to ensure the plant runs safely and efficiently, control room technicians monitor and control various aspects of the LNG facility, including pipeline flow rates, system pressures, temperatures and product quality.
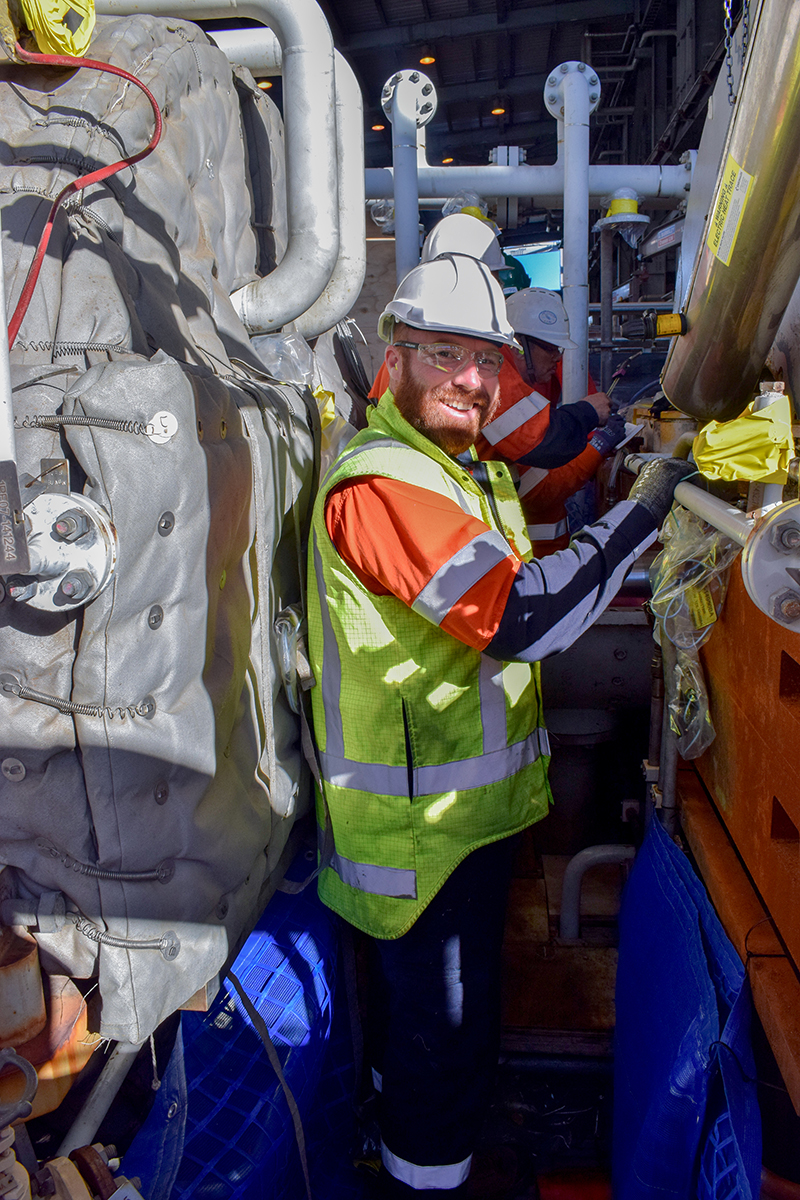
In real time, operators are notified of any components that require checking. All notifications are prioritized, and maintenance technicians promptly investigate and perform corrective work.
In any given month, maintenance workers respond to up to 300 corrective maintenance notifications across the facility, responding to everything from a flickering light to a faulty pressure reading on a transmitter.
Beyond just addressing immediate repairs, maintenance personnel carry out scheduled maintenance activities to guarantee the consistent performance and reliability of equipment.
ConocoPhillips schedules major maintenance events for intrusive work, such as maintenance on the facility’s 12 gas-fired turbines, which drive the refrigeration compressors at the heart of the gas liquification process. Such work can take from eight to 15 days.

“When we take a turbine offline for servicing, we scale down our production capacity by around 45 percent, so it’s important we make this process as efficient as possible, while also maintaining a relentless focus on safety,” said Maintenance and Reliability Manager Peter Long.
For every 8,000 hours of run time, Long said routine maintenance is carried out while the turbine remains intact. After 25,000 hours, he said, they conduct level two maintenance, where the gas generator section of the turbine is removed from the train for onsite hot section module replacement and internal component repairs if required.
“The turbines also have a major service interval at 50,000 hours,” he said, “where the complete gas generator and power turbine sections are removed and transported to the original equipment manufacturer in Houston or Italy for comprehensive servicing before being returned to our facility.”
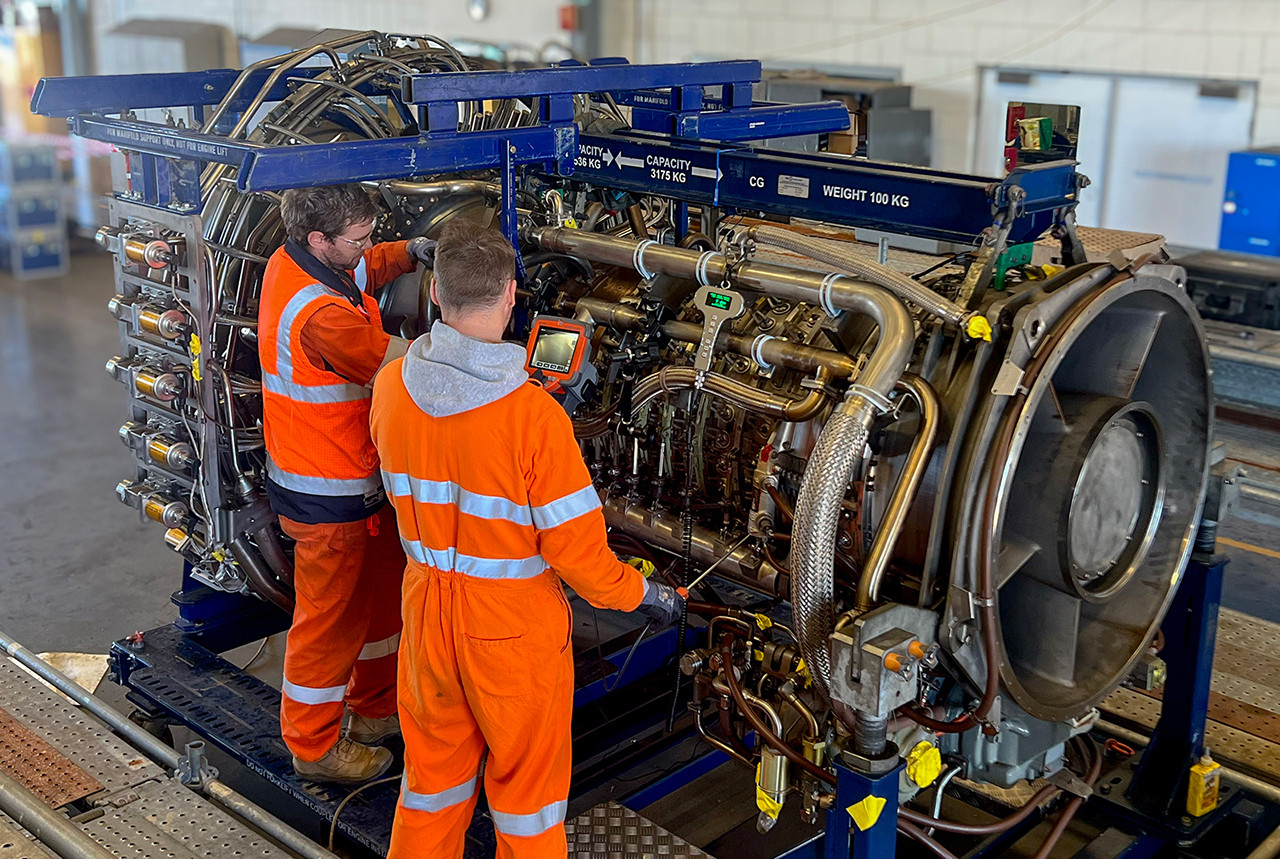
What is LNG?
Liquefied natural gas is a natural gas that is purified and cooled to -161 degrees Celsius to become a liquid. This process reduces its volume 600 times, which is like a beach ball being compressed into a ping pong ball.
The liquid is then loaded onto an LNG ship and transported internationally to a re-gasification terminal. At the terminal, the liquid is heated and turned back into gas.
APLNG Downstream Operations Manager Rune Tufta said workforce safety is paramount during maintenance and operational activities.
“We have an embedded safety culture,” Tufta said, “and our work is never so important that we cannot take the time to do it safely and in an environmentally responsible manner. We have a highly skilled workforce of technicians, engineers and maintenance specialists on site who are experts in safely leading scopes and complex maintenance events with precision and excellence.”
“In addition to focused Process Safety Interaction and Life Saving Rules Verification,” Tufta said, “we put additional measures in place to ensure the safety of our workforce during major maintenance events.”